What is Glass?
Glass is an amorphous, nonmetallic, and inorganic solid material obtained by cooling after melting. Glass is characterized by good optical properties, light transmission, transparency, high hardness, brittleness, poor thermal stability, and good thermal chemical stability. The unique glass also has special functions such as heat absorption, heat resistance, explosion-proof, bile, electric conduction, laser, and radiation protection.
Factory Direct Wholesale & Customization
1. Allocate Material
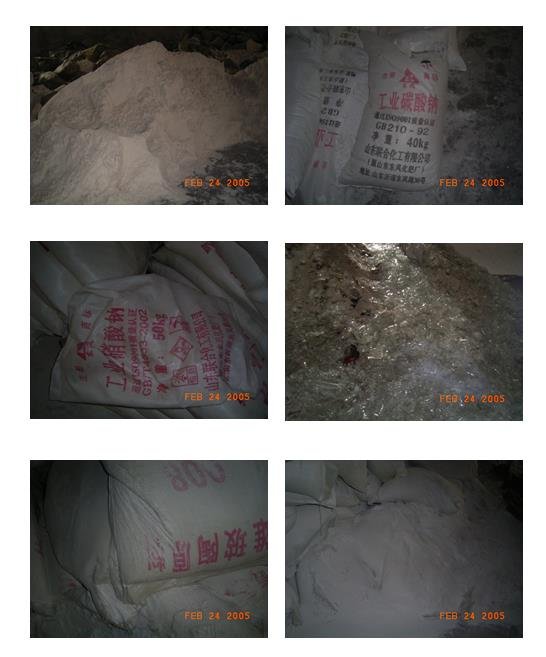
Raw materials for everyday use glass production :(the proportion of main components involves business secrets……)
- Silica sand
- Sodium carbonate
- Sodium nitrate
- Other auxiliary materials
- Broken glass finished material (the composition is the same as the production variety, accounting for about 20 ~30% of the total mixture)
2. Fusing Kilns
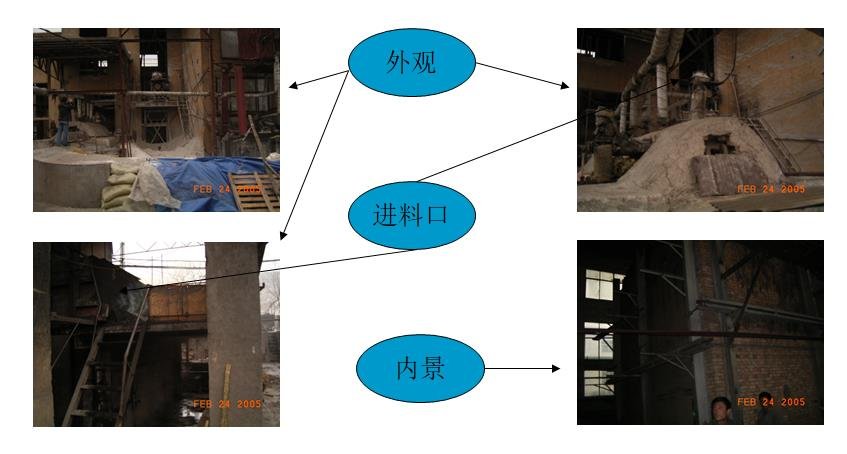
1. The ingredients are mixed in proportion based on a different product.
2. Melt into the furnace. The temperature of the molten material is about 1400 degrees
3. First Dip Blow Molding
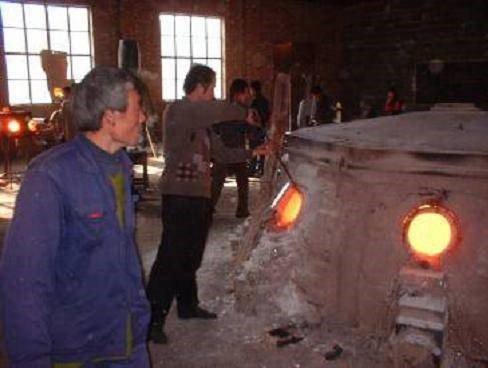
The manual blowing tool is a hollow iron pipe with a length of about 1.5m and a diameter of about 2CM. When blowing small products, it is only necessary to dip the material once. The specific amount of material declined depends on the product specifications. Blowing more oversized products should be based on the material used to develop the first dip well. Because the amount of the first dip directly determines the size of the blister.
4. Blow the vesicles and Second Dip Blow Molding
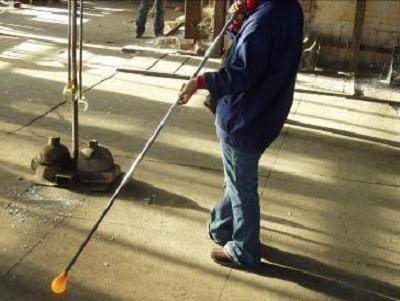
The primary purpose of blowing vesicles is to dip more material in the second dip. Because the iron bar is used directly to drop the material, the material is limited. Blowing large products, the material is not enough to use. And when you first blow into a blister and then dip, you can drop more material; the more extensive the blister, the more cloth you can decline. That’s what blowing vesicles is for Small bubble blowing is good before the second dip to hang cool, dry to 500-600 degrees (mainly by experience judgment), not too cold, not too hot. The double dip is easy to wrap into bubbles, and the giant bubbles of electric furnace products are generated from this link.
5 & 6: Airing The Small Bubbles & Second Dip Blow Molding
7. Roll the bell
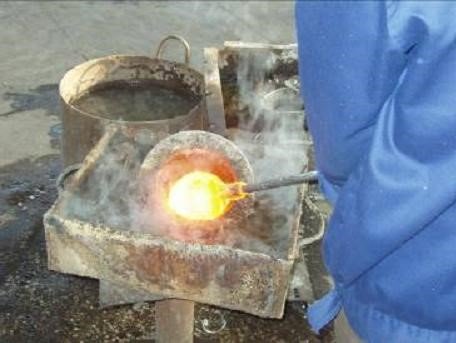
It is called a bell roll because the material is rolled in a thick iron bowl tilted in the sink after the second dip. The vast iron bowl is called the bell bowl. The purpose of a rolling bell is to make the second dip material uniform. To a certain extent, this treatment can solve the product wall thickness uneven, partial bottom, willow lines, and other problems.
8. Pounding Bottom
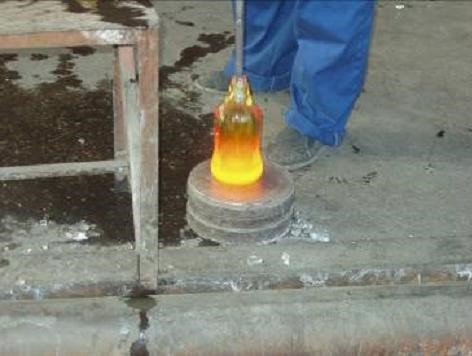
Pounding the bottom means the material is pierced on a thick, flat iron plate after rolling the bell and entering the Mold. This operation aims to make the inner and outer bottom of the product as smooth as possible.
9. Flattened
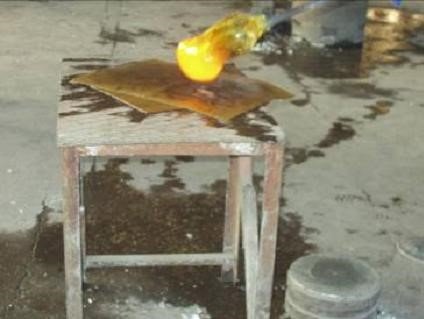
Pat flat on the straw paper with water a few times to make it a particular shape.
10. The Glass Put In The Mold
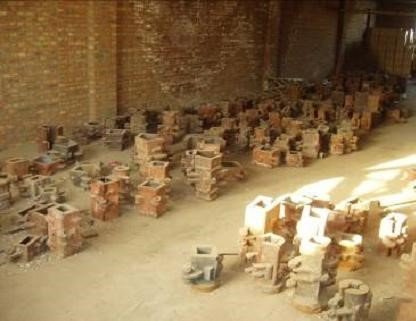
To make the product into the shape you want, you need to have the corresponding Mold, which is usually made of iron. The Mold needs to be smoked before use, and it is to brush a layer of tung oil on the Mold’s inner wall, then sprinkle with something like cork powder or bran skin. The purpose of smoking is to avoid Mold, and mold overheating will also lead to Mold, substrate, and other defects.
11. Hanging rod
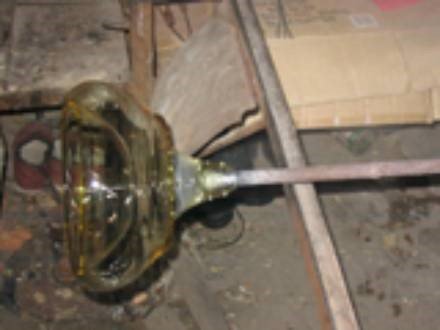
For the Just out of the Mold of the product, the temperature is still very high, and the material is soft. It is easy to deformation. So let it cool to a proper temperature before you put it in the kiln. Airing too cool, the product is easy to crack; Overheated, the product is easy to deformation.
12. Annealing
The glass is taken out of the Mold and placed in the annealing kiln for annealing. This process lasts about 4 hours, and the workers should control the temperature of the annealing kiln During this period. If the temperature is too high, the product is easy to deform, while if the temperature is too low, the product may burst.
13. Cutting the mouth
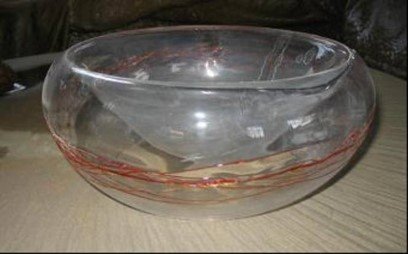
When the glass is out of the annealing ovens, the workers use an artificial diamond cut off the top of the hat and then cut it off with the fire. Please wait a moment, and the worker will manually separate them. Once these steps are finished, we will see a blank glass shape. This process is called cutting in glassware production.
14. Grinding
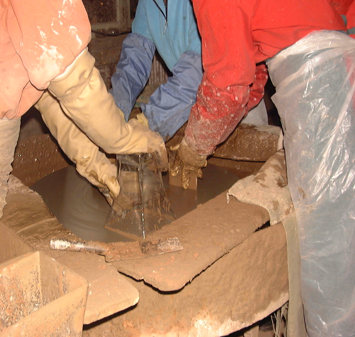
After cutting the product in the iron disk (diameter of 1.5 meters, built-in dilute into emery), grinding the mouth, determine the height of the product size, and ensure that the mouth is smooth.
15. Polished edges
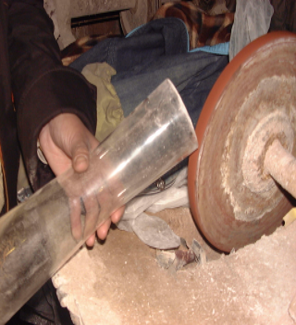
The edges of the mouth of the grinding product (inside and outside) are polished with the emery wheel. The product edges and corners do not appear to be a sawtooth phenomenon, and more can not be an advantageous edge to ensure consumers’ safe use.
16. Finishing Polish
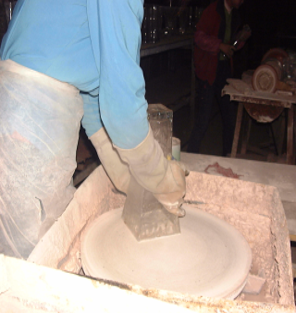
Take over the process, the product on the felt with the liquid polishing powder dissolved into the mouth surface polishing so that the mouth surface is smooth and bright and the color is the same as the product itself
17. Washing
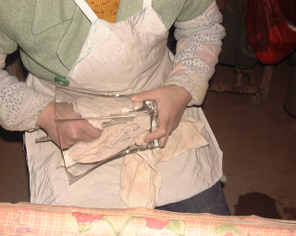
SCRUB the polished product in CLEAN water (twice) UNTIL there is NO FOREIGN matter on the product, then wipe dry with a clean cloth.
18. Packaging
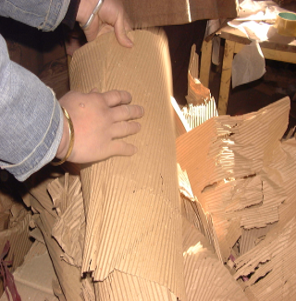
Packaging (stable packaging): After the above steps are completed, the quality inspection personnel shall carry out the overall inspection; Once passed, we will label and warp with bubble paper or white paper and corrugated paper into the inner box. And then put them into the master cartons.
For more details on the production process, please contact support@masshine.com
If you have any ideas, feel free to leave them in the comments section. Thank you for your time!